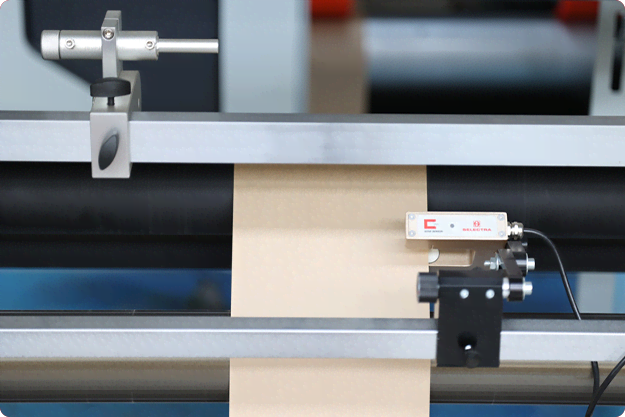
Quality Assurance
Ruizhi Machinery flat bottom paper bag machine, committed to international standards, ensures our equipment delivers unparalleled quality and performance, consistently setting the benchmark in the industry.
High Safety Standards
Ruizhi Machinery flat bottom paper bag machine, with a full-cover safety shield and automatic shutdown alarm, ensures safe operation while protecting the product from external interference.
Efficient Production
Ruizhi Machinery flat bottom paper bag machine, with its automated production line, produces 140 meters per minute, significantly reducing labor costs and enhancing productivity.
Modular Design
Ruizhi Machinery flat bottom paper bag machine, with the independent operation and coordination of modules (feeding, pre-punching, and bottom-folding) minimize downtime, streamline production, and ensure fast, efficient paper bag manufacturing.
Paper Bag Forming Drawing

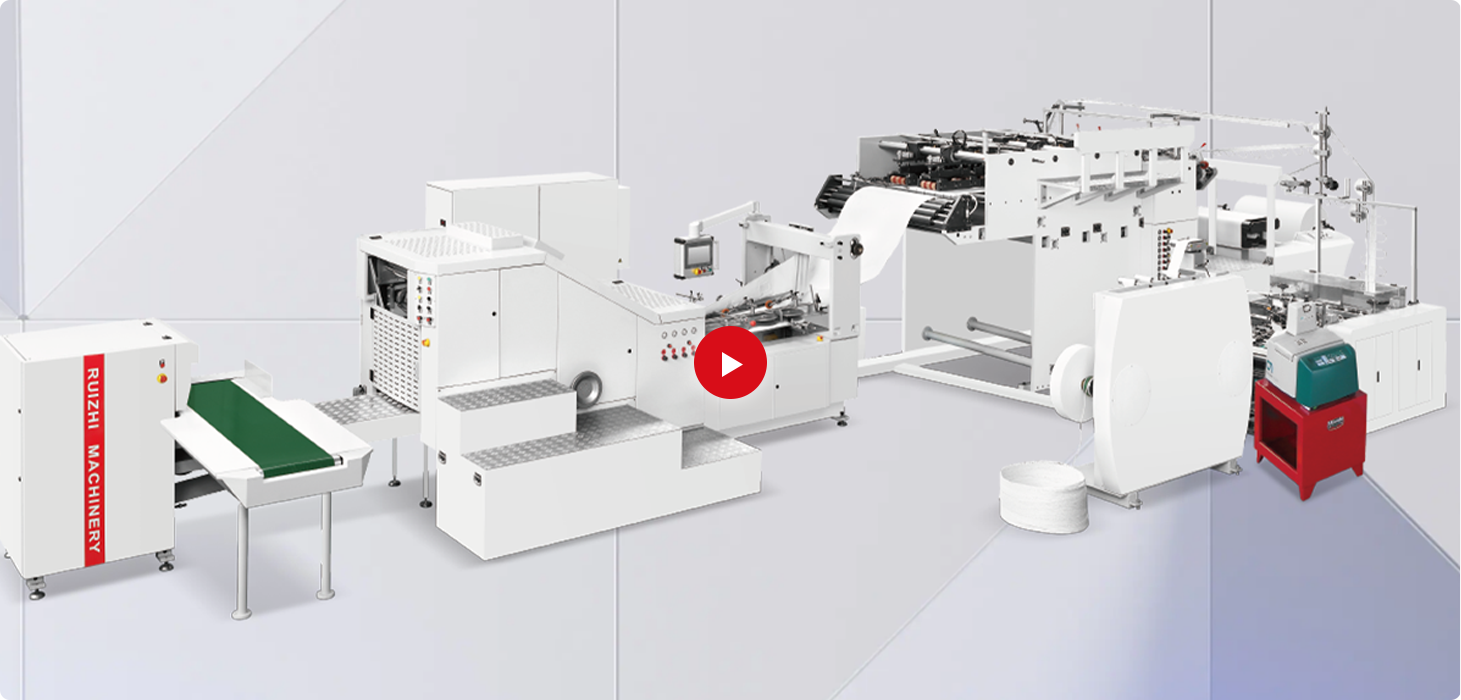
Specifications
Model |
RZJD-G350J |
Length of Cutting Bag |
600-1500mm |
Paper Bag Length |
600-1500mm |
Paper Bag Width |
70-350mm |
Insert Size |
20-120mm |
Bag Mouth Height |
15/20mm |
Paper Bag Speed |
20-180pcs/min |
Paper Feed Width |
160-960mm |
Paper Material Diameter |
1100mm |
Inner Diameter of Paper |
76mm |
Paper Material Thickness |
35-80g/㎡ |
Film Width |
80-280mm |
Rolling Film Thickness |
0.020-0.037mm |
Rolling Film Diameter |
500mm |
Working Air Current |
More than 0.12cubic meter/min,0.5-0.8MPa |
Machine Power |
380V 3 (phase) 4 (wire) 32kW |
Total Weight |
8000kg |
Machine Dimension |
11500×2500×1755mm |
Related Questions
Q:What is the purpose of this RFQ?
A:The RFQ aims to obtain specific quotes and details regarding after-sales service for the paper bag machine.
Q:What basic company information should I provide?
A:Please include your company name, the contact person's name, phone number, and email address.
Q:What equipment information do I need to specify?
A:Please provide the model of the paper bag machine, its production capacity, and the types of paper it can handle.
Q:What does the installation service cover?
A:Installation service typically includes the setup and adjustment of the equipment.
Q:What's included in the training service?
A:Training typically involves instructing operators on how to use the machine, and it's important to specify the content and duration.
Q:What about regular maintenance services?
A:Inquire whether they offer regular maintenance and how frequently it is scheduled.
Q:What's the response time for faults?
A:It's important to understand how quickly they will respond if the machine breaks down.
Q:How is remote support provided?
A:Find out the methods they use for remote tech support, such as phone or online assistance.
Q:What's the supply time for spare parts?
A:Inquire about the lead time for obtaining spare parts and their pricing.
Q:Is there an upgrade service for the equipment?
A:Inquire whether they offer upgrades or modifications for the machine and the associated costs.
Q:What's the customer feedback process like?
A:Ask how they gather and manage customer feedback.
Q:What are the main terms of the service agreement?
A:Confirm the specific terms and conditions outlined in the service agreement.
Q:Does the customer have any special service requests?
A:Verify if there are specific service quality expectations from the customer.
Request a Quote
We will deliver a solution and quote that best suits your business needs